King Production Line Safety Upgrade
Thermo Fisher Scientific’s journey to a safer production line
The Challenge: Overcoming Capping Line Safety Hazards
Thermo Fisher Scientific, a leading American biotechnology product development company, identified a critical issue with their bottle capping production line. The system was non-compliant with current safety regulations, revealing production line hazards that were a threat to their operations.
As safety regulations evolve over time, it’s imperative for companies to regularly reassess their systems and upgrade as necessary. The existing safety system on the bottle capping production line was found to be deficient in several areas:
- The machine guards didn’t sufficiently prevent access to hazardous points on multiple machines.
- Machines continued moving even after a guard had been opened, posing significant safety risks.
- There was a lack of integration between machines, and many emergency stop circuits were not up to the current standard.
Thermo Fisher Scientific partnered with Adbro Controls to address these capping line safety challenges and ensure compliance with the latest safety regulations.
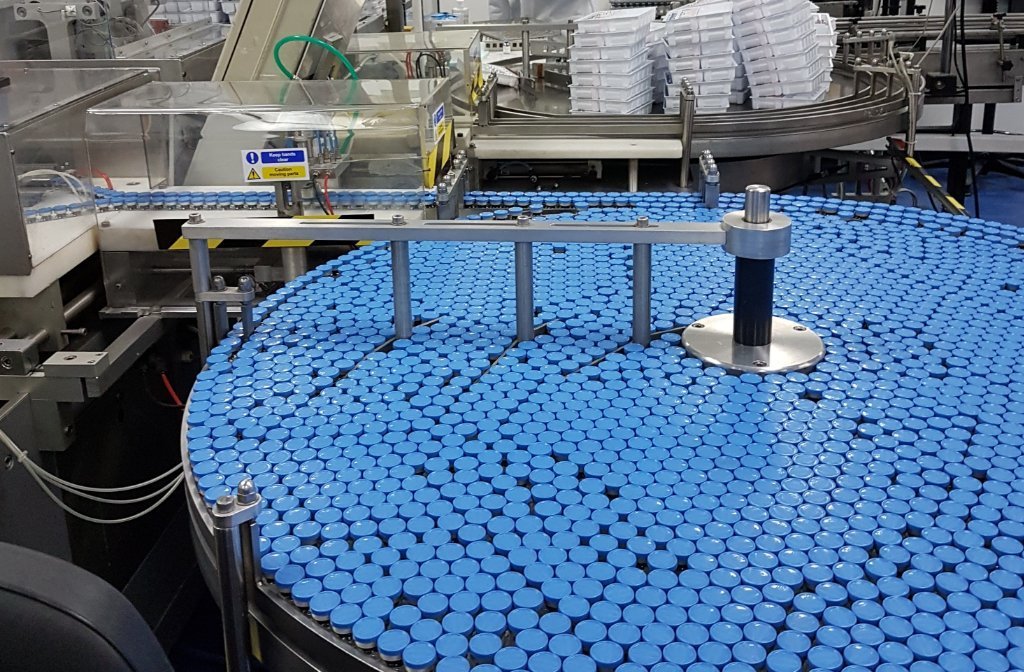
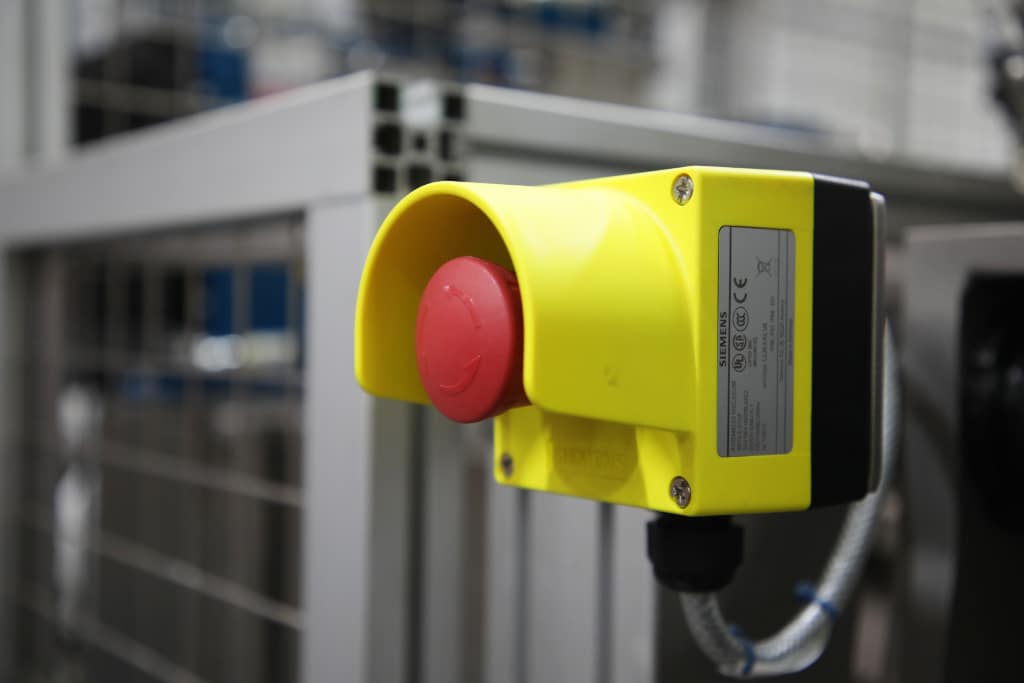
The Solution: Mechanical and Electrical Safety Upgrades
To address these safety concerns and attain safety compliance, Adbro Controls implemented a series of mechanical and electrical upgrades.
Mechanical Upgrades
Additional guarding was installed on sections of the line identified as hazardous. These guards were constructed using extruded aluminium profiles and polycarbonate sheets, ensuring strength and durability.
Moreover, pneumatic safety dump valves were installed on machines with actuators that could potentially cause harm to an operator. This proactive measure is designed to reduce the risk of injury.
In terms of installation, a basket was fitted across the ceiling to each machine’s cable drop for interfacing with the master panel. This design provided an effective way to ensure the integration of all machines, enhancing safety and efficiency.
Electrical Upgrades
The electrical upgrades revolved around the installation of a master panel that fed power to the entire line. This panel featured an isolating contactor, which could cut off power to all machines in the event of a global emergency stop, thereby safeguarding against potentially hazardous situations.
The heart of the master panel was a Pilz Multi-based safety control system. This system was designed to monitor local machine guard requirements as well as every emergency stop button on the field. It integrated a combination of remote I/O blocks for field devices and standard I/O for interfacing with each control panel.
An HMI (Human Machine Interface) was mounted on the master panel. This interface offered a diagnostic overview of the line’s entire safety system, allowing for rapid fault finding. Additionally, the HMI recorded alarms for fault tracking and implemented an integrated global stop test. This feature obliged operators to test the emergency stop buttons at fixed intervals, ensuring their functionality.
To further enhance safety, doors needing locking were equipped with a Pilz coded magnetic locking system. This system, along with the replacement of unsuitable guard switches with Pilz coded magnetic versions, ensured that all moving machinery parts would be completely stationary before guards could unlock. The old emergency stop stations were also replaced with Pilz buttons, featuring integrated signalling for quick diagnostics.
The Results: Enhancing Safety and Ensuring Compliance
Following the implementation of these mechanical and electrical safety upgrades, the production line saw significant improvements in terms of safety and compliance.
- Safety Compliance: A thorough SISTEMA report confirmed that the upgraded safety system was now fully compliant with current safety standards. This not only minimized production line hazards but also reduced the risk of potential legal complications related to non-compliance.
- Optimized Operator Interaction: The new guarding was designed to not be overly intrusive to operators during regular operations. Control of the master system was rendered intuitive, thus reducing the risk of operator errors leading to safety issues.
- Enhanced Diagnostic Capability: With the installation of the HMI, diagnostic information on each safety element on the line was readily available. This feature allowed for rapid fault finding when the system went into fault, ensuring minimal downtime and maximum productivity.
In conclusion, this comprehensive production line safety upgrade by Adbro Controls not only helped Thermo Fisher Scientific to address immediate safety compliance concerns, but also improved the overall safety and efficiency of their bottle capping line. By proactively managing potential hazards and integrating a system that offers thorough diagnostics and controls, companies like Thermo Fisher Scientific can continue their operations with the confidence that their production lines meet the highest safety standards.