Braze Detection and Rejection System
HydraForce’s journey of integrating automated quality control in their manufacturing process
The Challenge: Pursuing Automated Quality Control in High-Pressure Hydraulic Valve Manufacturing
HydraForce, globally recognized as the leading supplier of hydraulic cartridge valves, electro-hydraulic valves, custom manifolds, and electrohydraulic controls, confronted a formidable challenge in their inspection process at their Birmingham, UK production site. The key task was to ensure the consistent detection of a braze—a critical safety component—in their valves, which can handle pressures surpassing 3000 PSI.
The braze, a copper paste or ring, serves to fuse together distinct parts of the assembly. A fully completed braze ring is essential for safety compliance, as a deficiently brazed joint could potentially fail under high pressure, posing a risk of damage and injury.
HydraForce was seeking an advanced solution that offered both detection and rejection capabilities, aiming to segregate parts with incomplete or missing braze application. Furthermore, they desired a system that could handle minimal operator input, accommodating inspection of their 80 different components of varying sizes. A system capable of storing multiple ‘recipes’ or sets of instructions, easily changeable, was a must. And finally, they sought an ID marking feature for parts that pass the inspection, giving a clear indication of a successful process and present braze.
Yet, the true complexity of this challenge laid in its scale: the need to automate quality control in hydraulic valve manufacturing without compromising the efficiency and accuracy of the process.
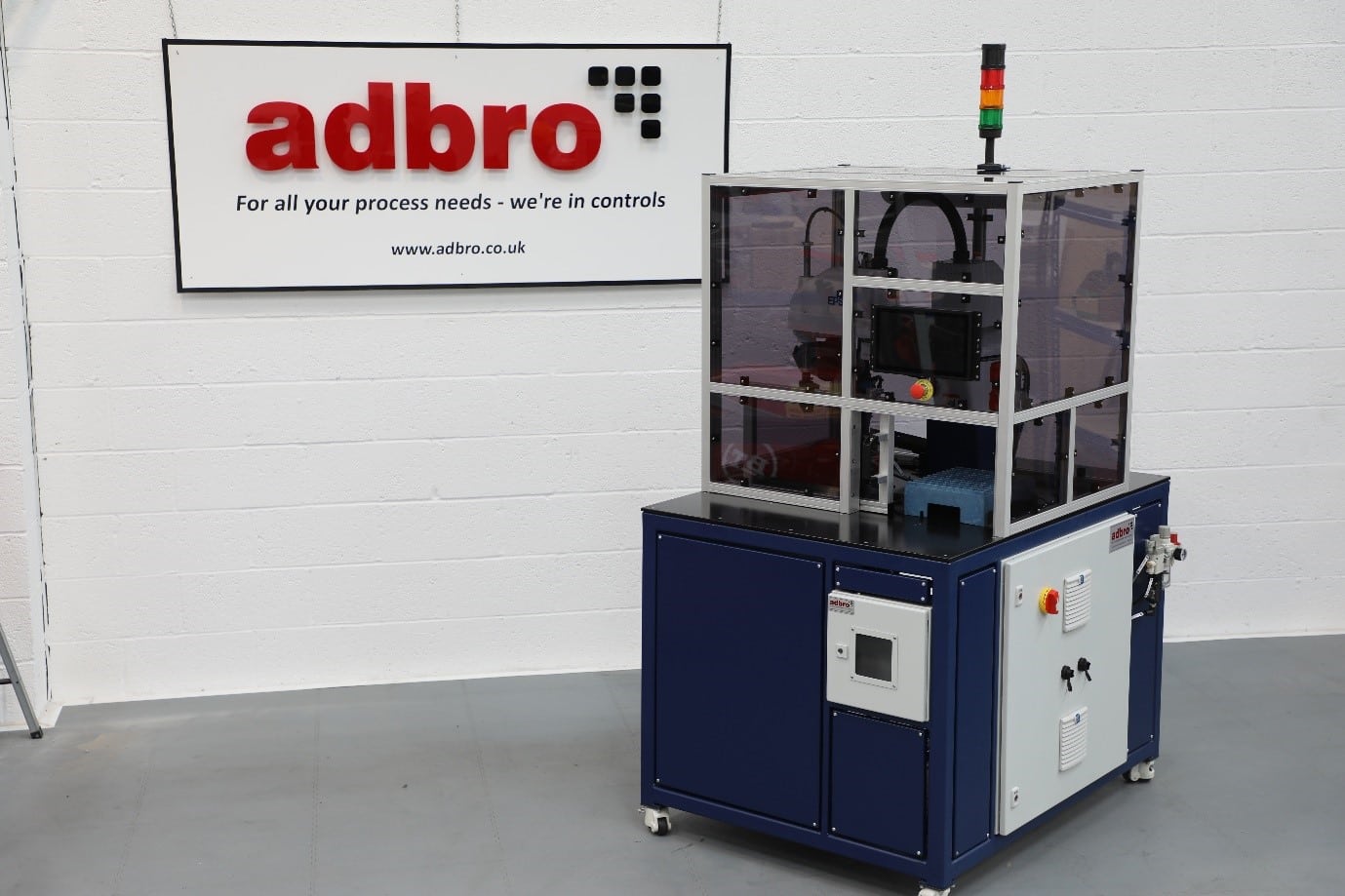
The Solution: A Standalone Detection and Rejection System
To meet HydraForce’s specific needs, Adbro Controls proposed a standalone detection and rejection system requiring minimal operator input. This solution consisted of a robust mild steel frame and incorporated sliding magnetic lock cell doors for easy access during pallet placement and removal. The system’s main components included an Epson T6 SCARA robot, sensors, pneumatic actuators, cameras, lenses, and strategically placed lighting. To meet HydraForce’s rigorous production and inspection demands, two of these systems were constructed.
A Human-Machine Interface (HMI) recipe system allows the operator to select the type of part to be inspected. Once a part type has been chosen, the operator loads the parts in a pallet into the system. The robot picks each part from the pallet and moves it to the inspection point. Dual cameras inspect the top and bottom braze for any potential gaps. Furthermore, the system checks the central tube of the part for an engraved ring at the top, an indication of incorrect assembly.
Here is a brief overview of the process:
- Inspection: The robot presents each part to the Sick 2D vision PICO cameras, where it’s spun 360° with an image taken at every 60°. This ensures a thorough inspection of the braze to distinguish good from bad parts. The top camera is mounted on a linear slide that adjusts according to the size of the part being inspected.
- Stamping: If the braze is present and the assembly is correct, the robot moves the part into the stamper. The stamper marks the part to indicate that it has been inspected.
- Rejection: If the braze is missing, incomplete, or the part is incorrectly assembled, the robot initiates the reject sequence.
- Final Inspection: A final inspection ensures that the part was successfully stamped before being passed to the outfeed.
For safety considerations, miniature photoelectric sensors by Sick UK Ltd. are incorporated to prevent potential collisions with the Epson T6 SCARA robot. If these sensors detect any tolerance issues, they halt all movements and trigger an alarm, prompting a check for recipe or pallet inconsistencies.
This all-in-one solution offers robust automated quality control in hydraulic valve manufacturing, streamlining the inspection process with impressive efficiency.
The Result: Enhanced Efficiency and Quality Assurance
Upon installation of the two automated quality control systems, HydraForce experienced significant enhancements in their inspection process. Prior to delivery, the systems underwent thorough in-house testing by our engineers at Adbro Controls. This pre-emptive measure reduced installation and commissioning time at HydraForce’s facility, enabling them to quickly integrate the new process into their operation.
The advanced quality control system provided by Adbro Controls has proven to be an invaluable addition to HydraForce’s inspection process. The time taken to inspect pallets has greatly improved, and HydraForce can now successfully inspect at least 800 parts per hour. This efficiency has not only ensured high-quality control in hydraulic valve manufacturing, but also cleared all pallets awaiting inspection much faster than before.
Key Highlights
- Efficiency: The automated system has significantly increased inspection speed, allowing for the inspection of at least 800 parts per hour.
- Reliability: Comprehensive inspection, stamping, and rejection sequences ensure that only parts that meet safety standards make it past the quality control stage.
- Versatility: The system can adapt to inspect 80 different components, thanks to the easily changeable ‘recipes’.
- Safety: Enhanced safety features, such as photoelectric sensors and automatic stops, ensure that the system operates smoothly and safely.
These results clearly demonstrate the transformative potential of automated quality control in hydraulic valve manufacturing. By integrating advanced technology into their operations, HydraForce has set a new standard in efficiency and quality assurance, making them a benchmark for others in the industry.
Working with the team at Adbro was a great experience. The level of support during and after the project was great. The whole team were very driven to develop and build the best system possible to meet our requirements.
The automation systems installed by Adbro have greatly improved our efficiency at inspecting parts.