Twin Pack Infeed Retrofit
An intelligent retrofit solution for a dynamic packaging line
The Challenge: Manual Labor in Packaging Lines
Pladis, the multinational biscuit and confectionery company, was facing a challenge in their Jacobs cream crackers packaging line. Their existing conveyor setup required manual handling of the crackers. The single packs were manually grouped into pairs and then transferred onto another conveyor. While this arrangement functioned, Pladis recognized that there were opportunities for improvements in efficiency through automation.
The concept of a complete replacement of the packaging line was ruled out due to cost and time constraints. Thus, Pladis and Adbro Controls agreed on a retrofit for the existing setup, identifying it as the most cost-effective and efficient solution to enhance their production line.
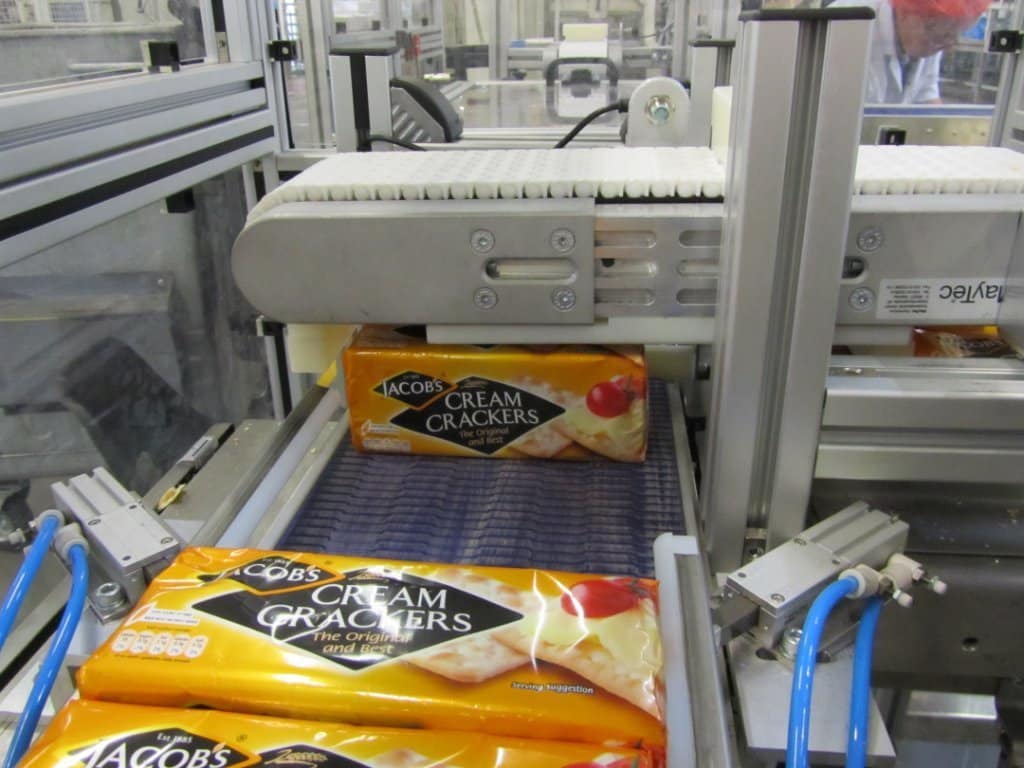
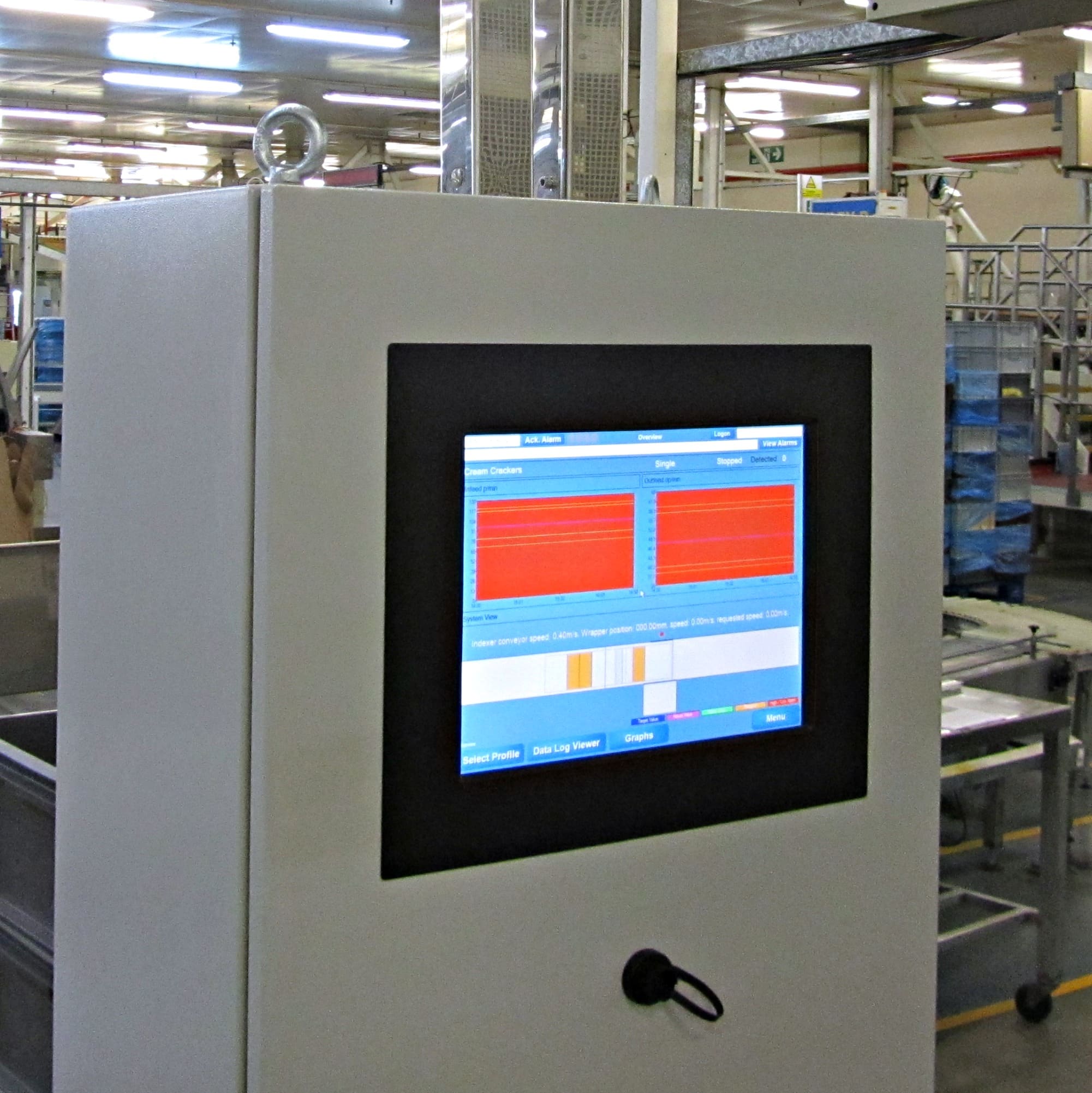
The Solution: Leveraging Automation for Twin Pack Infeed Retrofit
At Adbro Controls, we analysed the requirements and developed a bespoke automation solution for Pladis. The heart of the solution was to retrofit their existing conveyor system to be adaptable to both single and twin packets of crackers.
Adaptable Conveyors
Our team of experts introduced modifications to the existing conveyor setup, installing two additional conveyors, pack stops, and a divertor. This system eliminated the need for manual sorting of the packets. The pack stops were designed to control the flow of crackers when in twin pack mode, opening to allow two packs to pass through to the diverter, which was positioned at 90 degrees.
Vision Technology Integration
To automate the separation process further, we employed vision technology. A Basler camera monitored the cracker packets as they moved along the conveyor. The pack stops were programmed to respond to the positioning of the crackers, as detected by the vision system, both before and after the pairing.
Encoder and Logix PLC
We used an encoder to set the spacing between the packets, ensuring no overfill or delays. The encoder was controlled by a compact Logix PLC.
User-Friendly HMI
We also installed a Human-Machine Interface (HMI) to allow the operator to switch between three different modes for the infeed conveyors.
- Mode One: Allows a single pack to run at a set speed along the existing conveyor, passing under the new conveyor and straight into the case packer.
- Mode Two: Specifically for twin packs, dividing them into pairs and then diverting to the flow wrap machine for wrapping.
- Mode Three: For manual maintenance, permitting the operator to control each section of the system independently.
The Results: Improved Efficiency and Reduced Manual Intervention
The automation and conveyor system retrofit introduced at Pladis’ packaging line have yielded significant production benefits. By streamlining their packaging process, Pladis can now prepare packets for the flow wrap in a quicker and more efficient manner than before.
- Cost Savings and Efficiency: One of the biggest wins was the elimination of the manual packet-separation process. This modification not only saved on labour costs, but it also enhanced operational efficiency, allowing Pladis to reallocate their human resources elsewhere in the production line.
- Versatility of the System: The versatility of our automated conveyor system offers flexibility to switch between single and twin pack modes swiftly. It also provides a mode for manual maintenance, giving full control of the system to the operator when needed.
- User Experience: The installed HMI ensures a smooth user experience, making it easy to switch between different modes of operation for the infeed conveyors.
In conclusion, our conveyor system retrofit has significantly improved the efficiency of Pladis’s packaging line, validating our commitment to providing intelligent automation solutions that make a tangible difference.
At Adbro Controls, we are proud of this successful collaboration with Pladis and are committed to creating more such success stories. If you’re looking to enhance your production efficiency with automation, feel free to get in touch. Let us help you find your tailored solution.